Holland Provides a Full of Line of GEMÜ Valves
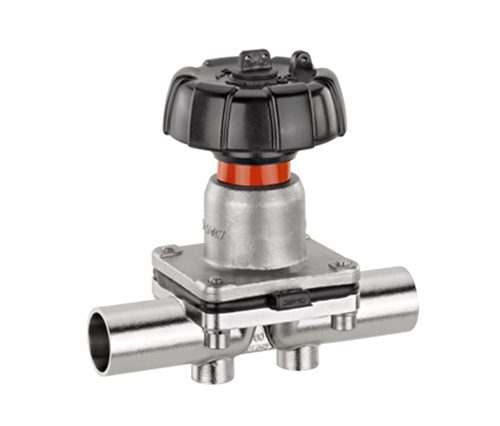
GEMÜ Metal Aseptic Diaphragm Valves
Metal aseptic diaphragm valves are primarily used in sterile applications in the pharmaceutical, food and biotechnology industries. Depending on the version selected, they are suitable for ultra pure water (Water for Injection), ultra high purity chemicals, intermediate and final products in the pharmaceutical and biotechnology industries, foodstuffs processing and the chemical industry. The valves can be sterilized and autoclaved within the bounds of their technical use parameters. Aseptic diaphragm valves are also used successfully as control valves in sterile areas.
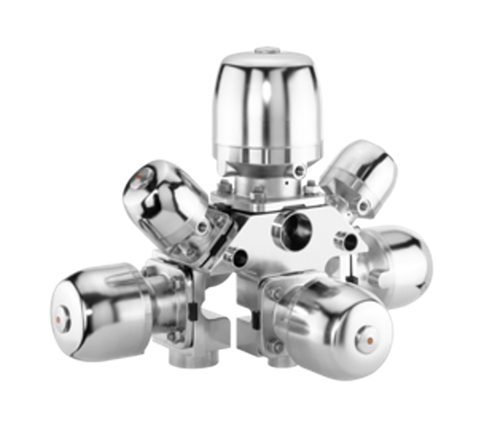
GEMÜ Multiport Block Valves
GEMÜ multi-port valve block systems are multi-functional units. At the same time, they minimize the number of fittings and welded joints, leading to a reduction of potential leakage points.
Combining functions in the smallest of spaces into one block offers even more advantages: The hold-up volume of media in the system is reduced in a measurable way, the flow is optimized and the size of a single plant is minimized. This enhances the performance capability of the entire system and reduces media consumption. Another advantage of blocks is that they provide junction points within plants. This simplifies cleaning and maintenance.
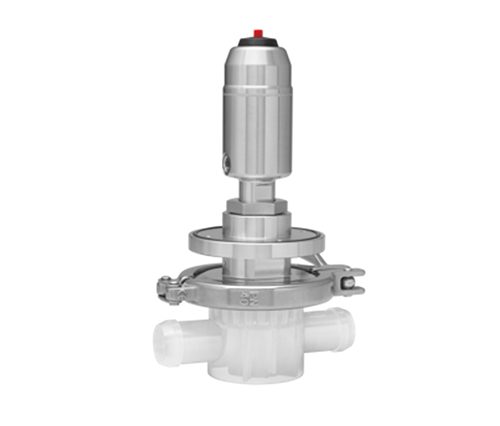
GEMÜ Single-Use Valves
The GEMÜ product range comprises single-use diaphragm valves with manual or pneumatic actuators as well as single-use pinch valves.
With the single-use diaphragm valves, the valve body is disconnected from the actuator and disposed of after it is used once. In contrast, the actuator remains in the system for multiple use.
The single-use pinch valves have a secured retainer, into which the tube is inserted. The tube is then compressed from above by a compressor to control and regulate the medium being conveyed. Thanks to the specially developed contour of the compressor, the strain on the tube is minimized. This increases the service life of the tubes.
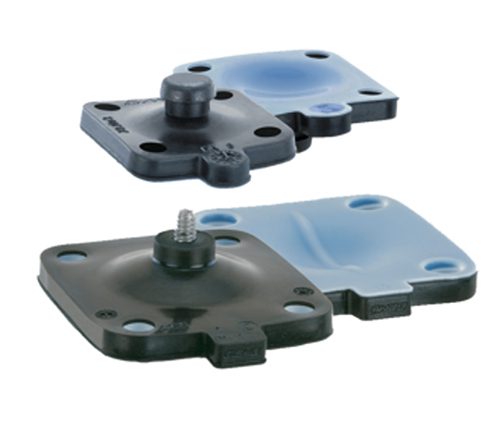
GEMÜ Diaphragms
Diaphragms are wearing parts. They need to be regularly inspected and replaced otherwise malfunctions can occur, possibly resulting in costly or hazardous situations. The maintenance intervals for inspecting and replacing diaphragms are application dependent. In order to determine a suitable maintenance interval, the maintenance history and the stresses placed on the parts due to frequent sterilization, cleaning processes or frequent duty cycles must be taken into account. The type of media must also be considered; the maintenance interval is considerably shorter for viscous or abrasive working media in comparison to inert liquids, for example.
GEMÜ developed its seal system for diaphragm valves with a sealing weir up to DN100 over three decades ago. A circular sealing bead in the valve body creates a defined external sealing point. This minimizes the ring-shaped gap between the diaphragm and the valve body and makes this seal system particularly suitable for applications in the pharmaceutical, biotechnology and cosmetics industries. Available in many options and materials; please contact our team for the latest and best diaphragm for your application.
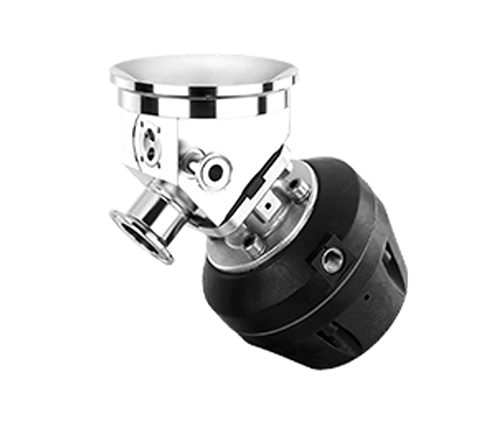
GEMÜ Outlet & Tank Valves
Tank valves are often welded to the lowest point in the base of the tank for use as outlet valves. This allows the tank to be fully drained, cleaned and sterilized. In addition to this, valves can also be fitted or welded to the tank cover, as well as fitted or welded to the tank wall.
Minimal deadleg – The unique sealing weir of the GEMÜ valve body sits very tightly against the tank wall, meaning that the dead space in the tank itself is kept to an absolute minimum. The geometry has been designed with special kidney-shaped contours in such a way that the tanks can be optimally drained, cleaned and sterilized.
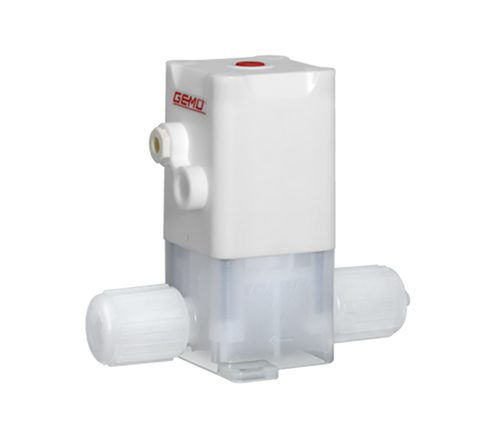
GEMÜ Diaphragm Globe Valves
Fast acting (200 mm/s), accurate (+/-0.5%) and repeatable (+/-0.5%) Gemu valves are available for aseptic, sterile or hygienic filling and regulating processes
GEMÜ has developed an innovative sealing concept for specific customer requirements. The unique feature of this concept is the PD technology seal (plug diaphragm technology), which ensures hermetic separation of the actuator from the product flow. The concept was then further developed specifically for sterile and hygienic applications.