S7 Weld Decay- Does your tubing and fittings pass the new ASME BPE testing requirements?
*Content for this post was sourced from an excellent article written by Carl Kettermann of United Industries. Holland is proud to offer United high purity process tubing and thank Carl for his contribution to the industry.
The 2019 edition of the ASME Bioprocessing Equipment Standard now includes a new welding requirement for stainless steel tubing. Found in Part MM – Metallic Materials of Construction, it requires that welded austenitic stainless steel tubing supplied to the industry must be capable of passing a weld-decay corrosion test and an intergranular corrosion test, as described in ASTM A249 and A270, respectively. These tests are being implemented to ensure that tubes, and the components manufactured from them, have been properly welded and heat-treated to provide optimum corrosion resistance in service. The requirement is stated as follows:
Austenitic stainless steel tube shall be capable of passing the weld decay test in ASTM A249/A249M, Supplement S7 and either the intergranular corrosion test in either ASTM A270/A270M, Supplement S1 or ISO 3651-2 Method B.
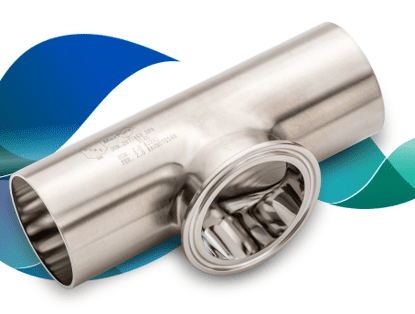
A VNE MaxPure fitting. Note that it is certified as being BPE compliant as indicated by the ASME symbol stamp.
The weld-decay corrosion test is often referred to as an S7 test and its purpose is to detect the presence of delta ferrite formed during solidification when welding austenitic stainless steel materials, such as 304, 304L, 316 and 316L. It should be noted that the BPE requirement is only applicable to the longitudinal seam welds made during the original manufacture of tubing. It is not applicable to the more highly alloyed materials like 317L and 904L or other super-austenitic materials because the nickel content in this alloy is high enough to suppress the formation of delta ferrite.
The presence of delta ferrite is a function of the chemical composition of the steel and the cooling rate of the molten weld puddle through solidification. Those welding processes that have faster solidification rates, such as laser welding, are less likely to form delta ferrite than a more traditional welding process like GTAW. This is because laser beam welds exhibit a smaller heat affected zone and smaller volumes of molten metal, and therefore typically exhibit better corrosion resistance. Delta ferrite increases the materials susceptibility to corrosive attack in reducing atmospheres, such as in hydrochloric acid, which is widely used in pharmaceutical manufacturing processes.
The ASTM A262 Practice E test referenced in ASTM A270 Supplementary Requirement S1 is often referred to as the Strauss Test and it is an intergranular corrosion test that detects sensitized structures that can form after improper heat treatment or after extended exposure to temperatures in the range of about 675 F to 1,000 F. Sensitization occurs when intermetallic precipitates such as chromium carbides are formed along the metal grain boundaries. When the chromium is bonded with carbon in these precipitates it is no longer available to form the passive chromium oxide layer that provides corrosion resistance.
Holland Applied Technologies has been one of the country’s largest suppliers of sanitary fittings and tubing to the biopharmaceutical industry for over 50 years. While there are many “bargain brands” available from all over the world, we have found that there are significant variances in quality and some producers fail to consistently meet the minimum requirements of the S7 and the Strauss test. Holland has taken significant steps to ensure that the sanitary ASME BPE fittings and tubing we provide meets the highest quality standards available. Should you have any questions on the ASME BPE Standard, or need help choosing your sanitary equipment, feel free to contact Holland Applied Technologies today.